Prefabricated Volumetric Modular Multi-Storey Structures
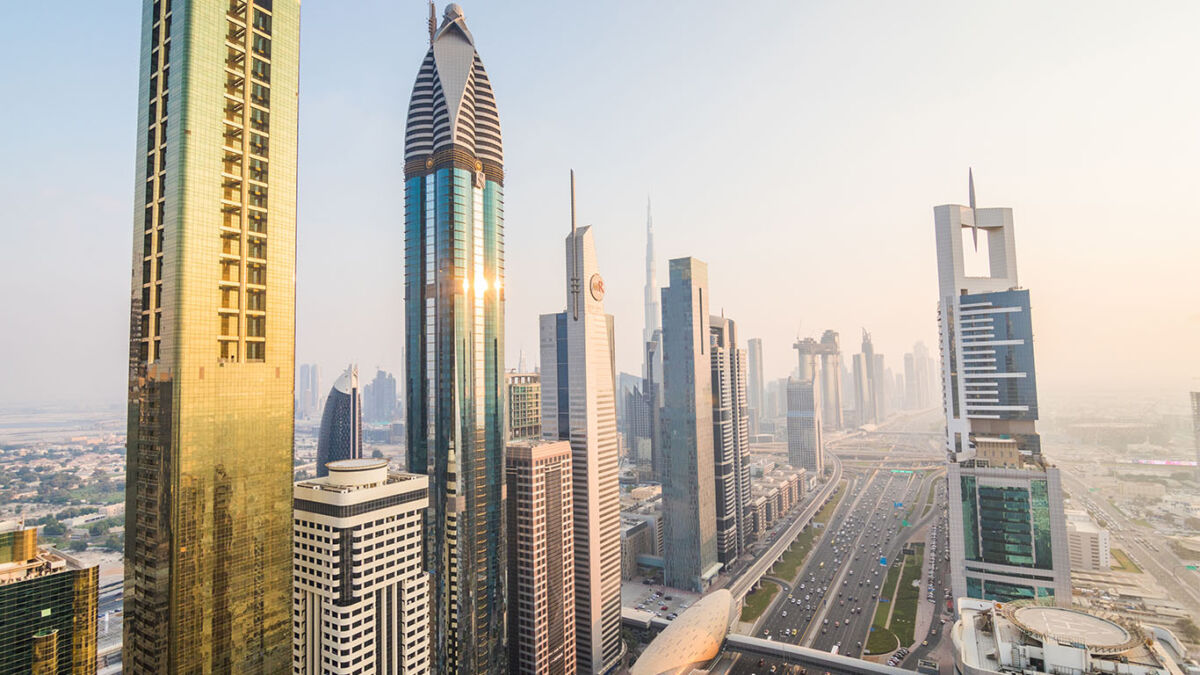
Modular high-rise buildings are buildings, usually 4 storeys and above, constructed using the modular construction method. Such buildings are created by manufacturing pre-fabricated modules (or components) in factories and then transporting them to the construction site and assembling them together.
Examples,
- Prefabricated Volumetric Modular Housing: Modular housing can include residential complexes or apartment buildings using prefabricated modules. Such buildings are used to construct a large number of housing units in a fast and cost-effective manner.
- Prefabricated Volumetric Modular Office Buildings: Modular office buildings are ideal for business owners who want to set up their workplace quickly. Modular offices can offer customizable interior arrangements and modern design options.
- Prefabricated Volumetric Modular Hotel Buildings: In tourist areas or other areas where demand is high, modular hotel buildings can be constructed. This allows hotel owners to expand quickly or add more accommodation units depending on the season.
- Prefabricated Volumetric Modular Apartment Buildings: Modular apartment buildings can be used to create high-rise residential units in densely populated cities and urban areas. Such buildings can offer solutions to housing crises.
- Prefabricated Volumetric Modular Trade and Shopping Centers: Shopping centers and commercial complexes can be built using a modular approach. This offers retailers the ability to quickly open new stores or expand existing facilities.
- Prefabricated Volumetric Modular Public Buildings: Modular construction can also be used for various public facilities such as public buildings, schools, hospitals, or administration buildings. Rapid construction can meet the need for public facilities needed in emergencies or in rapidly growing communities.
- Prefabricated Volumetric Modular Automation Warehouses: For the logistics and automation industries, modular automation warehouses or logistics centers can be used to meet rapidly changing storage and distribution needs.
The widespread use of modular high-rise buildings is characterized by the ability to speed up construction processes, increase quality control and achieve cost-effectiveness. However, they must be designed specifically for each project and comply with local building regulations and requirements.
What are the main features of prefabricated modular multi-storey buildings?
- Modular Design: This type of structure is built by assembling factory-produced modules or components. Modules are usually manufactured to standardized sizes and specifications, which speeds up the design and construction process.
- Fast Construction: Prefabricated modular buildings can be completed more quickly than traditional construction methods. Since the modules are prefabricated in the factory, they only need to be assembled when they are transported to the construction site.
- Quality Control: Since modular structures are manufactured in a factory environment, quality control can be better ensured. Each module is manufactured in accordance with factory standards, resulting in more consistent and high quality results.
- Customization Capability: Modular design can be customized to meet different needs. This enables structures with different functions to be built quickly, for example for residential, office, commercial or industrial uses.
- Portability and Expandability: Prefabricated modular structures can be dismantled and transported as needed or expanded by adding more modules. This means that the structures can be moved to different locations or enlarged as needed.
- Energy Efficiency: Modular buildings can have special design and material options to improve energy efficiency. This can lower operating costs and reduce environmental impact.
- Environmentally Friendly: Prefabricated modular buildings generally produce less construction waste and optimize the use of materials. They are therefore considered a more environmentally sustainable option.
- Cost Efficiency: Faster construction times and less material waste can make prefabricated modular buildings more cost-effective. It also allows for better control of the project’s budget.
- Low Labor Requirement: Modular structures can require less labor on the construction site than traditional construction methods. This can reduce labor costs.
- Diverse Applications: Prefabricated modular structures can be used for residential, commercial, industrial, healthcare, education and many more applications.
Thanks to these features, prefabricated modular multi-storey buildings can be an attractive option for many different construction projects. However, each project must be specially designed and comply with local building regulations and requirements.
According to the regulations and regulations in our country, prefabricated buildings with a maximum of 2 floors are allowed. Modern Methods of Construction (MMC), which we can call an alternative construction method, which is an innovative, sustainable, industrialized version of the construction sector in the world, has become a state policy with regulations in most developed countries such as England, USA, Canada and Japan. In recent years in Turkey, significant efforts and studies are being conducted regarding the design and implementation of light steel prefab and volumetric modular structures, as well as the modification and improvement of regulations. It is very important to take the necessary steps for the wider use of building technology in Turkey as soon as possible by making the necessary initiatives before the relevant authorities to revise the standards and regulations followed for the static and earthquake design of light steel and volumetric modular structures.